2016 Custom Safari Race Buggy (aka - Mad Buggy of Doom)
Originally built with a 2.1 VW flat 4 aircooled motor using running gear from a VW Beetle Baja racer, then converted to a Renault transmission and RX-8 rotary engine for a few years, now coming to the end of a conversion to a supercharged S2000 engine, along with many, many upgrades to suspension
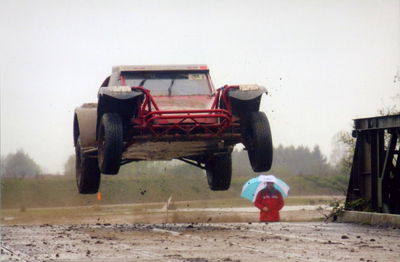
Originally built with a 2.1 VW flat 4 aircooled motor using running gear from a VW Beetle Baja racer, then converted to a Renault transmission and RX-8 rotary engine for a few years, now coming to the end of a conversion to a supercharged S2000 engine, along with many, many upgrades to suspension, brakes, etc, along the way.
Basic Performance Stats:
0-60mph - 4.6s (on gravel/dirt + M/T tyres)
0-100mph - 9.0s (gravel/dirt)
Top Speed - 137mph (runs out of gears)
Horsepower - 360-500+ (dependent on boost) 360bhp is the basic setup currently.
Torque - 250lb ft
Weight - ~800kg (including fuel, etc)
Power/Weight Ratio - 450+bhp/tonne
Current Specs:
Engine
- Honda S2000 (2.0L F20C), supercharged using an Eaton M112 sourced from a 5L V8 Jaguar, twin injectors, long-branch exhaust manifold, dry sump oiling system, custom wiring loom running on DTA S80 engine management.
- 9000rpm redline, approx 360bhp in low boost setup, circa 500+bhp available in high boost setup, if we ever find enough traction to use it…
- The engine has been rebuilt and intake and exhausts sized with that 500+ in mind however, just in case…
- Fed from a 20L fuel cell in the front of the car, through a Bosch 044 pump. Fuel cell contains foam baffling to reduce slosh and a rollover valve to prevent fuel flowing or venting in the event that the car rolls over for a belly tickle.
Transmission
A 30 year old UN5 transaxle sourced from a Renault Master van. Only the finest components used here! It has a strong gearset and a large final drive (5.85:1) allowing the use of the tall off-road tyres. Unfortunately, for some reason, Renault chose ratios that aren’t very good for racing with a 9000rpm capable engine, strange choice on their part. Basically that means 1st gear is redundant - it’s quite short and will only take the car to 30mph. So unless you really want to kill a set of rear tyres, it’s only use is for shunting around the pits and driving onto the trailer.
Actually 2nd gear is only much use in the deepest of power-sapping clay and peat terrain too - it will spin the wheels in 3rd up to 90mph or so if you wish…
In a similar fashion, a 5th gear that is great for fuel economy on a low-revving diesel van at 70mph on the motorway, is rather long when combined with 9000rpms, somewhere in the region of 165-170 is possible. But not when your aerodynamics are worse than a house-brick and it’s pushing 4 parachutes disguised as mudguards either corner, so 5th actually resides on a shelf, weight saving and all that….
Driveline
Okay, onto the boring bits for the gearheads, greasemonkeys, and those of you who’ve just had way too much caffeine today:
The clutch is a hybrid, using the S2000’s flywheel, but machined and faced on the lathe in order to take the pressure plate (uprated with a stronger diagphram spring for more clamping load) and friction disc from a 200SX - this gives a 230mm instead of a 215mm disc for a little more torque capacity, and the friction plate is a 3-puck cerametallic paddle type for minimum MOI.
The main reason for the swap is that switches the assembly to a push instead of pull clutch to work with the Renault gearbox and release bearing - that does mean of course that you need to put the Renault input shaft into the 200SX’s friction plate - so the centre spline has been replaced on the plate to suit.The input shaft is also machined to suit the end support bearing in the engine - and then shortened too because we’ve cut and rewelded the gearbox back together in order to shorten it and push the engine forwards for better weight distribution.
The differential is a standard open one, mainly because nobody seems to make performance plate diffs for Renault commercial vans - gap in the market there - and it feeds into a set of GKN Porsche 930 CV joints which have been uprated with chromoly internals and remachined cages so that they are much stronger and will do more angle than a standard joint.
These are fitted to spring steel driveshafts which are specifically designed to twist like a torsion bar to take out shock loadings from the drivetrain and prevent gearbox damage, and at 31 inches long they didn’t come particularly cheap, but they’re a vital part of keeping the car reliable.They feed into our own billet aluminium uprights at the rear, which are made to have a pair of wheel bearings so big that the CV joint feeds clean through the middle of them and virtually bolts to the wheel itself - that’s to allow those shock-absorbing shafts to be as long as possible, and reduce the angle seen by the CV joints to reduce wear and allow lots of suspension travel at the rear.
The wheels are Mitsubishi Shogun/Pinini as they have loads of offset and are fairly light, but they used to be steel wheels we made ourselves - which is what is on it in the action shots, 16x7J at the rear and 16x6J fronts, shod in 235/70 and 195/70 Fedima EvoExtreme (competition soft compound) tyres.
Brakes
- Front: 290mm 2-piece ‘wavy’ discs, clamped on by Hispec 4-pot calipers acting through Carbotech XP8 pads.
- Rear: 310mm 2-piece ‘wavy’ discs, Wilwood 4-pot calipers with Carbotech XP10 pads.
- Hydraulics: Tilton pedal with brake bias adjustment working through a pair of 0.75” Wilwood master cylinders, pressure reduction valve in the rear.
The rear brakes have independent ‘fiddle’ brake cylinders which allow the sides of the car to be braked independently. Braided steel hosing throughout.
All the calipers are fitted with low-retraction seals and anti-knockback springs behind the pistons to keep the pads snug up against the disc - even with all the vibration and shock encountered - to keep the brake travel consistant.
As for the discs, there are a few reason the discs are scalloped as they are
- Firstly the shape means they pump debris, mud, water away from the pad surface in bad terrain, to keep the brakes biting well.
- Secondly they tend to improve initial bite (at the expense of pad life) because of the extra leading edge biting in, especially when cold.
- Thirdly although the disc itself runs hotter than a normal one, the air pumped over the pad surface keeps pad temperatures down during sustained downhill braking, especially when using the fiddle brakes. Working that the other way around with bigger discs and softer pads results in more weight when you don’t need it, but it only works if you have spare heat capacity/don’t need as big a brake as you can fit in the wheel.
And the most important reason is of course that they look funky ;)
They’re all homemade - discs, bells, hubs, etc, etc, so is the anti-knockback kit in the calipers.In terms of other bits, we also run a valve in the rear line that can reduce hydraulic pressure - which means that the brake bias is altered depending on how much grip the car has at that moment in time - and the independent rear cylinders means the car can be slewed around the rear wheel in tight forest tracks or used as a pseudo-LSD by manually braking the inside wheel out of tight corners.
Chassis/Suspension
Tubular steel spaceframe to MSA/FIA regulations, made from T45 seamless tube which is similar to American chromoly DOM, but a bit stronger and better from a welding perspective.
Front Suspension:
- VW Beetle-derived twin trailing arms, 4” longer and 3” wider arms than standard, custom made from T45 with altered geometery.
- Chromoly uprights and oversized king and link pins, upgraded bearings and bushes
- 6082-T6 billet aluminium hubs to suit Mitsubishi wheels/stud pattern.
- Fox Shox monotube coilover, 10 inches of travel, with modified internals, custom valve stacks and currently fitted with Bilstein remote canisters currently but will be hydraulically interconnected using Penske canisters shortly.
- Twin springs in a tender setup, with rising rate polyurethane foam bumpstops for big hits.
- Total front travel is approx 12-14” depending on settings.
Rear Suspension:
- VW Beetle-derived rear trailing arms, approx 6” longer and 4” wider than standard, custom made from T45 tube. Altered geometery to make it a semi-trailing arm.
- 6082-T6 billet aluminium upright and hubs, bolt on with shims for setup adjustment.
- 2 x Fox Shock monotube coilovers per side, 12 inches of travel, modified internals/valve stacks and all fitted with Fox remote canisters.
- Single spring setup, rising rate geometery, foam bumpstops, the rear also has a pair of torsion bars on rocker arms that can be engaged at any point in travel, and adjusted to provide a flat jump in spring rate or a progressive ramp near full compression travel for rougher terrain.
- Rear travel 17-18” depending on geometry settings.
Interior/Electronics/Bodywork
- 2 x Motodrive composite bucket seats, vinyl covers for mud/dirt resistance, no sexy alacantra here unfortunately.
- 2 x TRS 3” strap 5-point harnesses.
- 5083-T6 aluminium bulkheads front and rear of the cockpit, sealed with fireproofing compound.
- 2mm thick 6082-T6 aluminium main floorpan, separately replaceable overlapping skidpans/floor armour in vital places, ranging from 5mm (front beam protection) to 12mm thick (centreline of gearbox/engine sump)
- 2 litre AFF fire extinguisher between the seats.
- Wiring loom is all custom made, running water proof plugs with silicone gel shielded contacts, main loom is wrapped in ptfe to allow it to move with the vibration without rubbing through, then oversheathed with abrasion-resistant fibreglass braid. Copper overshield woven through the fibreglass to reduce electrical interference.
- All instruments and dashboard switches are sealed against moisture using a liquid PVC compound.
Dash instrument gauges consist of:
- Boost Gauge
- Oil Pressure Gauge
- Oil Temperature Gauge
- Water temperature Gauge
- Couple of idiot lights for the driver for oil pressure/temp/alternator charge (gauges are the codrivers side so as not to distract driver)
- Everything else (TPS, MAP, RPM’s, Charge temps, etc) is datalogged through the ECU.
A bespoke fan control unit allows soft starting and speed control of the twin 16” engine cooling fans to reduce the strain on the electrical system when they first start up (80+ amps startup current).
- Electrical system hard cutoff switches either side of the car (inside and out).
- Side panels, front and rear bonnets, etc, are made from 1.2-1.5mm 5082-T6 aluminium sheet, all hand formed, which is why it looks like it fell out of the ugly tree and hit every branch on the way down. Yes, all those rear louvers were hand made. No, we don’t want to do it again, we’re still having therapy.
- Side gullwing doors/windows are 4mm polycarbonate, Marguarded to attempt to stop them marking up so much, front windscreen is laminated glass with an extra internal laminate layer.
- Mudguards are HDPE supersingles from a truck - cheap, lightweight, flex out of the way of those trees that give you a hug and meet the regulation specs for sizes - apparently nobody specified “pretty”.
- Front and rear wings are custom high downforce profiles, made the old fashioned way with spars and tubes to give them a lot more damage resistance than a skinned foam wing. Top skin varies from Diolin/Kevlar up front for gravel rash resistance, to fibreglass and/or Solartex on the rear depending on the element. Required upgrades as the front wheels used to lift off the floor at 120mph+
Theoretically we can generate up to 400kg of downforce @ 100mph but untested as yet. The car itself probably generates 200kg of lift by then though….
09/05/2017
- Added more pictures as we’ve now re-made the dashboard so it looks a bit neater - and it gets the mounts out of the way for those new paddles behind the steering wheel….:D
- The last of the hydraulic plumbing has gone in, and the steering rack has been rebuilt/upgraded with some proper bearing strip rather than just being steel running on the ally casing, less wear, less slop and less friction this way, so the steering feel and feedback should be better.
- As you can see in the photo’s we’ve also ditched the off-the-shelf set of fiddle/steering brakes and I’ve modelled and made my own, they’re a little bit light, MUCH stiffer for less flex in the controls, and all the joints and pivots are bushed so they also have less slop, less wear and less friction, and they now use more widely available Wilwood cylinders instead of the CNC Brakes ones which were, well, crap.
It’s been a while as we’ve been waiting on some new parts coming for the dashboard which were ordered 5(!) months ago and have just turned up today!
- As you can see in the photo’s we’ve also ditched the off-the-shelf set of fiddle/steering brakes and I’ve modelled and made my own, they’re a little bit light, MUCH stiffer for less flex in the controls, and all the joints and pivots are bushed so they also have less slop, less wear and less friction, and they now use more widely available Wilwood cylinders instead of the CNC Brakes ones which were, well, crap.
20/12/2017
- Yep, long time between updates, but there’s been a lot happen that meant we haven’t had much time on the car, however, I’ve updated with new photos off all the alterations to the loom to suit the new dashboard, and what it looks like now it’s nearly finished.
26/01/2022
- Has it been 5 years already?! Whoops.
Hey look, it’s painted, it’s been to the dyno (got a few fuelling niggles to sort, back there in a week or so) - and it moves under it’s own power!
Updated with a pic and a new video below!
There’s probably more I’ve forgotten that should be in that section so any specific questions please ask so I can answer them here
To Follow Shortly, when I have less RSI
- Fleshing out of basic spec lists with details and history
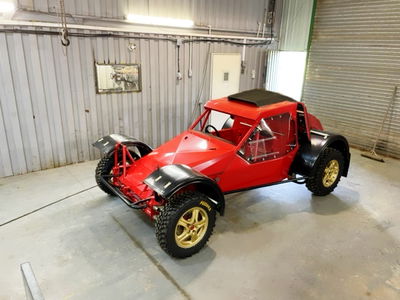
No longer have to sit in the seat making vroom noises:
— MadBuggyOfDoom (@MadBuggyOfDoom) September 14, 2018
Told you it was about time @the_oily_one pic.twitter.com/aXDpP96Qzh
Comments
Jesus H vac…….
Is Jesus H banned on Steam?
It looks awesome!
Right, I’ve fleshed out most of it, although I need to go back through because I’ve ended up with about 4 different styles on the spec lists. I’ll start adding some build history to the bottom of it it later, but are there any specs/components anyone wants to know/know more about before so I can make sure everything is on the spec lists?
Updated with basic performance info.
Added another vid with the rotary engine in.
Wow awesome
Thanks, it’s good fun, well, when it’s not in the workshop for years having a rejig anyway!
Added a couple more event photo’s I just found.
Updated again, 09/05/2017
(For the americans scratching their heads, I’m from the future!)
Updated, 20/12/2017 - Not added much bar pictures of the new dashboard and looms.
13/06/2018 - Updated, more photo’s added to gallery - wiring finished, new dashboard powered up, new fiddle brakes, gearlever, side panels, etc.
Pagination