Engineering Explained: How The Koenigsegg Regera Hypercar Drives Without A Gearbox
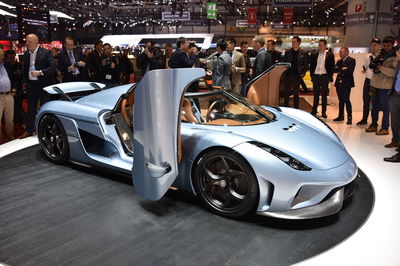
When it comes to transmissions, the car community can be a bit picky. The general consensus seems to be that manuals > DCTs > Planetary Autos > CVTs. CVTs get a lot of unwarranted hate, despite the fact that they’re quite efficient, have been used in Formula 1 (and were banned), and based on my own experience are far better suited for paddle shifters than planetary autos. Regardless, Koenigsegg has said enough with this debate, and has removed the whole thing for its new Regera hybrid hypercar. No rev matching, no millisecond counting, and no elastic feel. Just a direct link between the engine’s hydraulic coupling and the rear axle. To understand how this system works, let’s first go over the components involved.
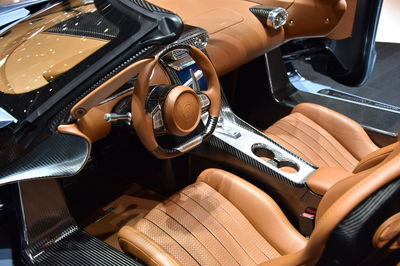
Battery
Yep, it’s a hybrid. A 620 V 9.27 kWh battery rests between the two occupants allowing the car to run on pure electric (up to 50km) if desired.
Electric Motor/Starter
Resting between the battery pack and the engine, a 160 kW (~215hp) motor mounts up to the engine crank, acting as a starter motor, but more importantly providing additional torque to the crank, especially useful when the engine is at low speeds.
Engine
A 5.0-litre twin-turbocharged V8 engine producing 820 kW (~1100hp). Peak power is reached at 7800rpm, while redline is at 8250rpm. The engine has a desirable torque curve, producing 1000 Nm (738lb ft) or more from 2700 to 6170rpm.
Hydraulic Coupling
There seems to be little verbiage about this currently, but by definition a hydraulic coupling is a device which uses a fluid to transmit mechanical power. This coupling has the ability to both open and close, meaning the output shaft can be connected or disconnected from the power sent from the engine’s crank. The wording seems to be attempting to avoid comparison with a locking torque converter, which is certainly how this device is described as acting.
Final Drive
Power is sent to the rear differential which has a final drive ratio is 2.85:1. This is the only gearing between the engine and the wheels, and the gearing does not change.
Driveshaft-Mounted Motors
Each of the rear wheels have driveshaft-mounted electric motors. These motors produce 180 kW each (~240hp), and are what initially provide torque from a standstill.
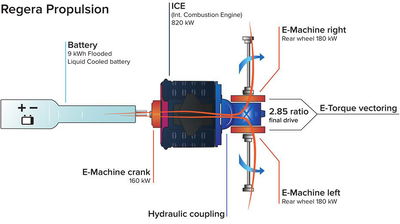
The process of reaching the top speed:
1. The two electric motors on the rear axle start acceleration, pulling their energy from the car’s battery. The hydraulic coupling is open at this stage, so the engine can charge the battery if necessary, but does not provide any power to the rear wheels. Why not? At this point, the vehicle is traction limited, so putting down more power is not an option. The Regera reaches 62mph in 2.7 seconds, which is pretty impressive considering it’s RWD only.
2. As the speed of the vehicle increases (from 0mph) the hydraulic coupling begins to close up. This means not only is the engine providing torque to the rear wheels at this time, but the crank-mounted electric motor is as well.
3. At around 30mph, the hydraulic coupling can lock up, so now the engine is directly driving the rear wheels without the interference of a transmission. 30mph correlates with about 1000rpm. Where does 1000rpm come from? Here’s some maths:
(30mph)/(((((345mmx0.30/(25.4 mm/in))x2+(20 in))x(pi))/((12 in/ft)x(5280 ft/mi)))x(60 min/h))x(2.85) = 1021 RPM (crank speed at 30 mph).
Essentially, you’re trying to calculate the number of times the tyre rotates (345/30R20 size) at 30mph, and then this number is multiplied by 2.85 (the final drive ratio) to determine the engine speed.
4. Once the hydraulic coupling is closed up, the car will reach its top speed once it reaches the engine’s redline at 8250rpm. It’s really that simple!
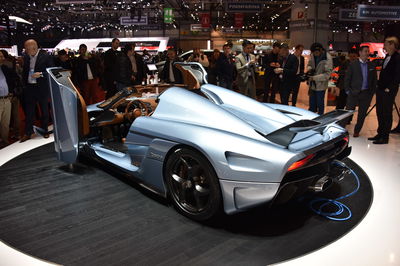
So why use a system like this?
- Since the vehicle is traction limited from a standstill, engine use at low vehicle speeds is not needed, and the engine produces so much power (in combination with the electric motors) that a gear reduction for additional wheel torque is unnecessary once higher speeds are reached.
- Parallel hybrid systems will have additional energy lost through the transmission linking the engine to the wheels. A direct drive allows for less energy loss through the drivetrain.
- Series hybrid systems convert energy from mechanical to electric, and back to mechanical. These conversions waste energy; KDD does not operate this way.
If you’d like some additional detail (including maths), and would like to hear me mouthing Swedish words, check out this video:
Comments
No comments found.