What Are Reverse-Flow Engines?
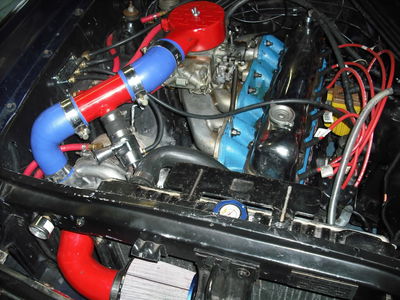
Engine layouts have some general common factors that translate from one setup to the next, making spotting the different components within the engine bay fairly simple once you know what you’re looking for. You can follow the trail of internal combustion, starting with the air intake, air box, through to the inlet manifold, injectors, engine block and then finishing with the exhaust manifold on the right.
But there is a niche group of powerplants that blow this traditional layout to pieces and do things their own way: reverse-flow engines.
Most engines out there have what is called a cross-flow head, which has the inlet and exhaust ports located on different sides of the engine block. Traditionally, the inlet valve is situated to the left of the cylinder, with the exhaust valve found on the right. This means that the gasses within the engine have to travel across the head from inlet to outlet, hence the name.
So, reverse flow heads do the exact opposite, with the inlet and exhaust ports situated on the same side of the engine. This means that the gases have to enter the head and then turn on their heels when being pushed back out by the engine’s exhaust stroke. So why would an engineer switch the tables like this when the cross-flow head is so embedded in the automotive psyche?
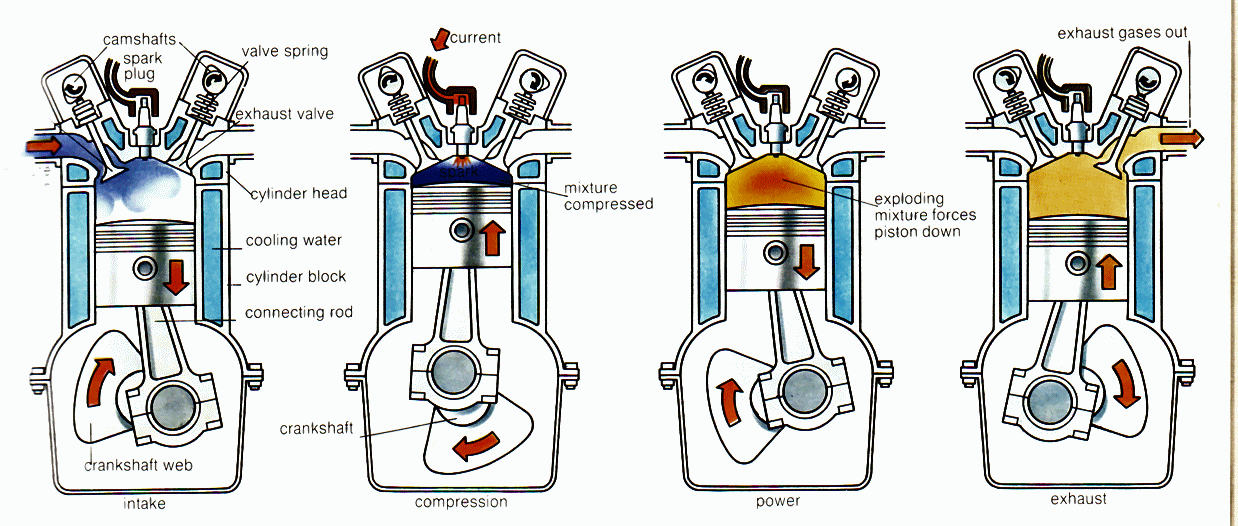
The main advantage of a reverse-flow head is to do with exhaust scavenging. In case you didn’t know, exhaust scavenging is the process of forcing the exhaust gasses out of the cylinder as much as possible to make room for the intake air in the next cycle. To maximise the volumetric efficiency of an engine, the aim is to get as much of the exhaust fumes out of the cylinder to the exhaust manifold to make as much room as possible for the intake stroke sucking in the fresh air and fuel.
In a cross-flow head, the swirl of the intake air has to cross the cylinder head which reduces the quality of mixing and the scavenging efficiency during the exhaust stroke. The swirl of the inlet air is much like the water in a toilet spiraling when you flush. So during overlap (when the intake and exhaust valves are partially open at the same time) the air has to switch directions to make it across to the exhaust port. In a reverse-flow head, the air can keep swirling in the same direction as it makes its way to the exhaust port, improving scavenging.
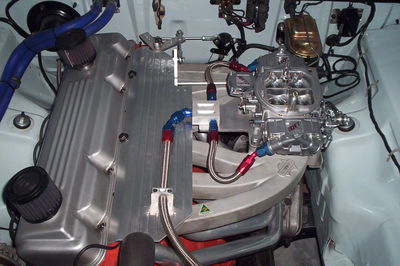
A reverse-flow head can also make an engine much cheaper to make, as the intake and exhaust manifold can be cast as one lump of metal rather than splitting them up to be placed on either side of the block. Another advantage is an improved performance when it comes to cold starts, as the intake air is slightly heated by the exhaust gases leaving the engine block close by.
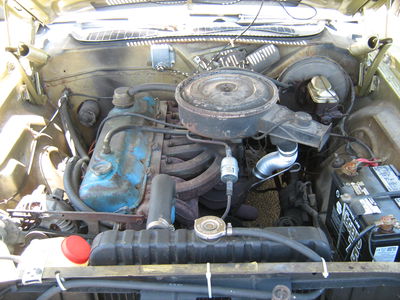
Unfortunately, that heating becomes one of the main downsides of a reverse-flow system. For maximum thermodynamic efficiency within an engine, the aim is to have as larger a temperature difference between inlet air and the temperature of combustion. A nice cold intake makes the air dense, meaning more can be crammed into the cylinders which creates more power. Unfortunately, having the exhaust manifold so close means that the intake air will inevitably have some heat transferred across to it, reducing the efficiency of the engine cycle.
In addition, the ports in and out of the engine normally need to be reduced in size to squeeze in both the intake and exhaust on the same side of the engine block. This therefore decreases the volume of air that can enter and leave the cylinders, restricting performance in comparison to a cross-flow engine. To combat these drawbacks, engineers cleverly staggered the intake ports to sit slightly higher than the exhaust ports, rather than keeping them in a straight line. This allows much more space for the ports to be machined to their full capacity.
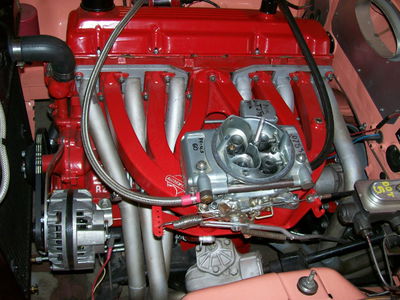
For modern day relevance, the Scuderia Cameron Glickenhaus racing team has been using a 4.4-litre reverse-flow V8 in its SCG-003 track-based road car, following on from the team’s entries into numerous endurance races. The car utilises the exhaust port reconfiguration to pump out 600bhp and 738lb ft of torque. The company is about to release an ‘S’ variant of the endurance racer for the road which bumps power up to 750bhp and should be able to achieve 217mph along with a sub-three second 0-60mph time.
The tech was also used on Holden six-cylinder engines and Leyland Minis but never really managed to get a foothold in the mass-production of cars due to the sacrifices in overall efficiency.
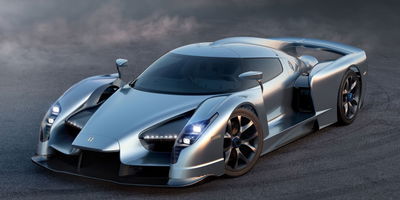
Although reverse-flow heads are super rare in the car world, the engineering principles behind their manufacture still hold true to this day. And seeing the technology still being used in racing and road car applications, the heyday of the reverse-flow engine may still be yet to come. They have their issues, but with the efficiency of the IC engine still being relatively poor, maybe reverse-flow engines deserve another shot at the big time.
Comments
Why is this even an article, these are conventional heads ad they were being used forever, the entire crossflow head idea is the new fancy thing. Pretty much any inline engine before the 70s used the conventional head layout, probably because it was easier to do all the machine work on one side.
And the comment about siamese ports, that is more about the layout of the valves being laid out in order so the intake or exhaust valves of adjacent cylinders being together so the ports can be integrated.
My daily has a reverse flow head.
Love seeing those ‘Aussiespeed’ intake manifolds !! in American cars no less !! Aussie built Chryslers from the 60s and 70s were a very powerful car that were so cheap to buy for us new drivers here in Australia in the early 80s loved them !!
I would hope someone does an article about Scuderia Cameron Glickenhaus’ car wink wink nudge nudge.
Reverse flow head on my dads 1964 f100 223 inline 6
Awesome post! Learned something new today!
Pagination