Engineering Explained: Clutch Basics And Performance Clutches

The clutch is an integral part of a manual transmission, and despite the fact we can use it hundreds of times during a trip, for many people there’s still some mystery surrounding the way it works. So today we’re going to answer four questions surrounding clutches:
- What is a clutch?
- Why do clutch discs have internal springs?
- What is a performance clutch?
- Why would you need a performance clutch?
1. What is a clutch?
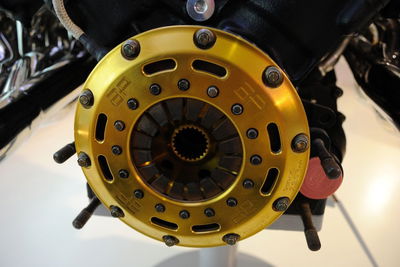
As the name implies, there’s some grasping going on here. The clutch is the connection point for the engine and the transmission; the torque converter of manual cars. It’s made up of several important components:
Clutch Disc
The clutch disc is splined to the input shaft of the transmission. The disc itself rests between the flywheel and the pressure plate, both of which rotate with the engine. So the clutch disc is spinning with the transmission, and on either side of it is a metal surface which rotates with the engine.
Flywheel
For the purposes of a clutch, a flywheel is the mating surface through which torque is transferred. It’s one of the two sides the clutch disc is sandwiched between. The flywheel is connected to the engine crankshaft and always rotates with the engine.
Pressure Plate
The pressure plate is the other side of the sandwich around the clutch disc. It is bolted to the flywheel and rotates with the engine, and inside it houses the diaphragm spring.
Diaphragm Spring
When you depress the clutch pedal, this is the spring which is removing pressure from the clutch disc. A throwout bearing is used to press against it, and it creates a gap between the pressure plate and the flywheel, allowing the clutch disc (and thus the transmission) to rotate freely.
2. Why do clutch discs have internal springs?
You’ll often notice springs within the retaining plate of a clutch disc. These serve to dampen and smoothen out the engagement of the clutch disc, and they help absorb any fluctuations in engine RPM. As power strokes are not a continuous event, the rotational speed of the flywheel has slight variations in speed which are transmitted to the clutch disc. If this continues to the transmission, it can result in unrefined power delivery as well as audible rattling of the gears. The clutch springs help smoothen out this speed difference, so the transmission sees a more linear power delivery.
This is very similar in theory to a dual mass flywheel, which eliminates torsional vibration sent to the transmission through springs as well, but a DMF reduces the vibration before it ever reaches the clutch disc.
3. What is a performance clutch?
Performance clutches typically involve heavier springs and different disc materials. Using a heavier spring will result in a clutch with more clamping force, meaning more torque can be transmitted without the clutch slipping, and the clutch will be much more likely to grab under aggressive shifting or clutch dumping.
Different materials will result in drastically different characteristics for a clutch. Organic compounds are more common for production vehicles, as these allow for smooth engagement and long life, but they don’t necessarily work well at high temperatures. Kevlars, carbons and ceramics will offer intermediary smoothness, while being able to operate at higher temperatures.
Often, performance clutches will use “puck” designs with gaps between the clutch disc blocks. I believe there’s a bit of a cool factor here taking priority over functionality, however there is some logic to it as well. With less surface area the pressure on the clutch material will be higher, and some materials will provide more grip at certain pressures. The force transmitted by the diaphragm spring will be the same, but the pressure on the clutch disc will be higher. In some cases, this can be beneficial. That said, on the highest powered engines I’ve ever seen, the clutch discs used are full circles will small cutouts for heat expansion.
Speaking of high power, if you’re going all out you may find yourself in the territory of sintered iron clutch discs. These discs will work at exceptionally high temperatures in comparison to other materials, and can handle extremely high clamping forces. Of course, drivability is nearly eliminated, as it becomes much more of an on/off switch than a clutch pedal with modulation.
4. Why would you need a performance clutch?
Performance at high temperatures
Performance clutches become necessary when the power levels or temperatures experienced by the clutch system exceed the levels at which the stock clutch disc can operate. If the clutch is getting excessive use, such as a track day, it may not be able to withstand the heat. Over time, it will begin to fail to grab, and this will result in it only getting warmer. As the disc temperature rises, it works less and less, until finally failing or allowing it to cool. If between shifts it has a hard time grabbing, even when at operating temperatures, it’s likely that the clamping force isn’t high enough for the power levels.
Launch control
For drag vehicles, the clutch needs to be able to grab well during a launch. If it’s slipping too much you may need heavier clamping force. If some slip is desired during launch, it’s important to select a material which can handle the heat.
Your econobox is fine
Like most modifications, upgrading a clutch disc is something which is application specific. It’s important to understand that while an upgraded clutch may mean you can transmit higher power levels and run the clutch for longer durations, it also may make engagement poor. One of the biggest benefits of organic materials is that engagement is smooth, and this helps you control the clutch pedal better and makes every day driving much more manageable. Even under more heavy use, organic compounds and stock clutches can often handle some track use with proper technique. If the clutch grabs fine, engagement is smooth, it doesn’t slip, and performance is consistent with repetitive use, rest easy knowing all is well.
Comments
No comments found.